A lot of rhodes electric keyboards I've played have terrible action,
usually sluggish and bouncy. I've installed some mods on mine
from vintagevibe.com which transformed it
into something very playable:
- Miracle Mod
- Back Check Mod
- New Hammer Tips
Most of the techniques for installing this stuff can be found in youtube
videos from vintage vibe. But there are a few techniques I found that
can help out as well.
Miracle Mod
The miracle mod is by far the most important mod for improving the
rhodes keyboard action. This mod places a small bump between the key and
the hammer making the contact area between the two smaller. This makes
it so there is less friction between the two parts giving a faster and
lighter action. Keep in mind this mod should be done BEFORE the back
check mod. I didn't do it this way and had to re-adjust all my back
checks since the hammers actually sit a little higher up with the
miracle mod.
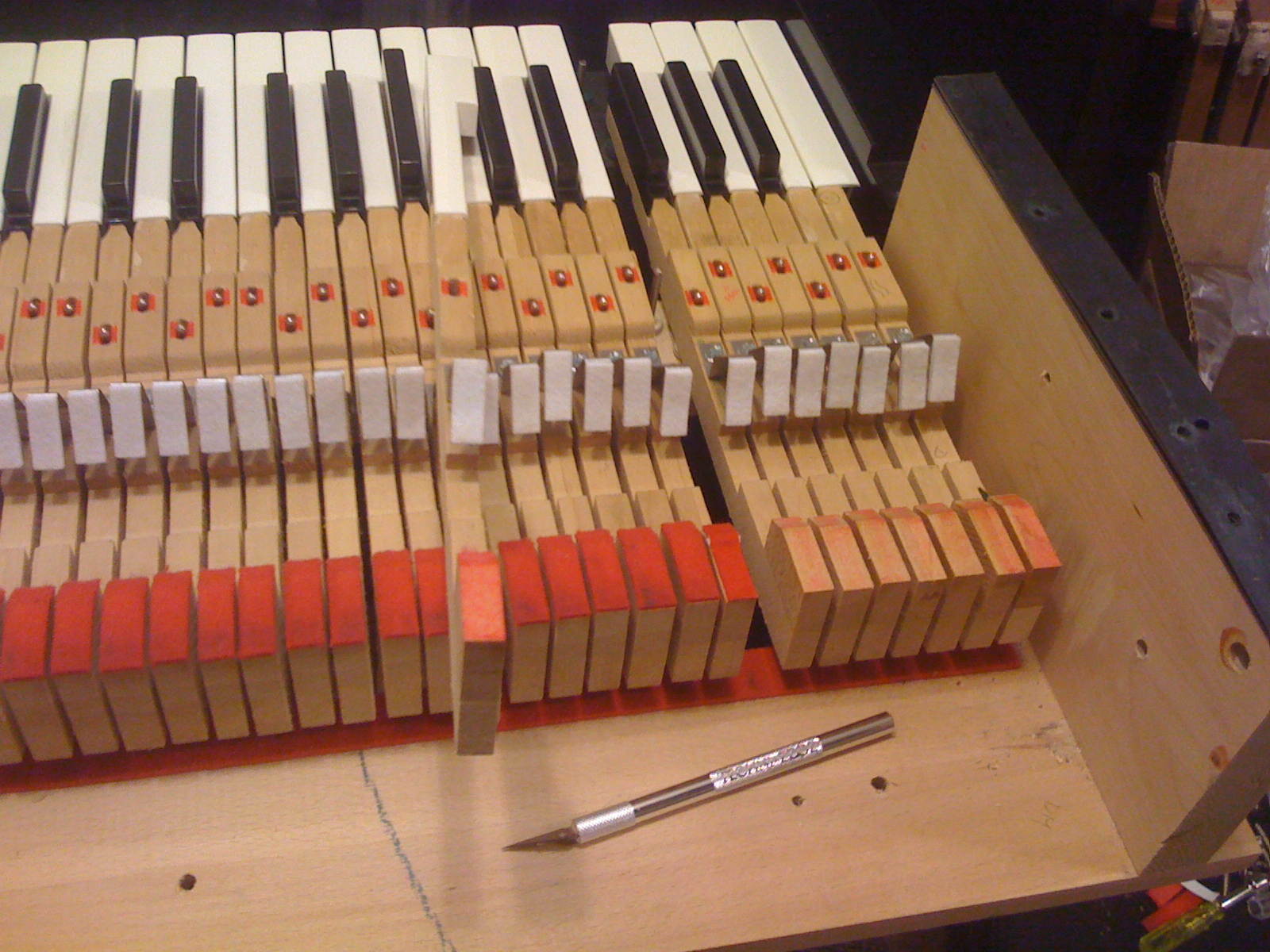
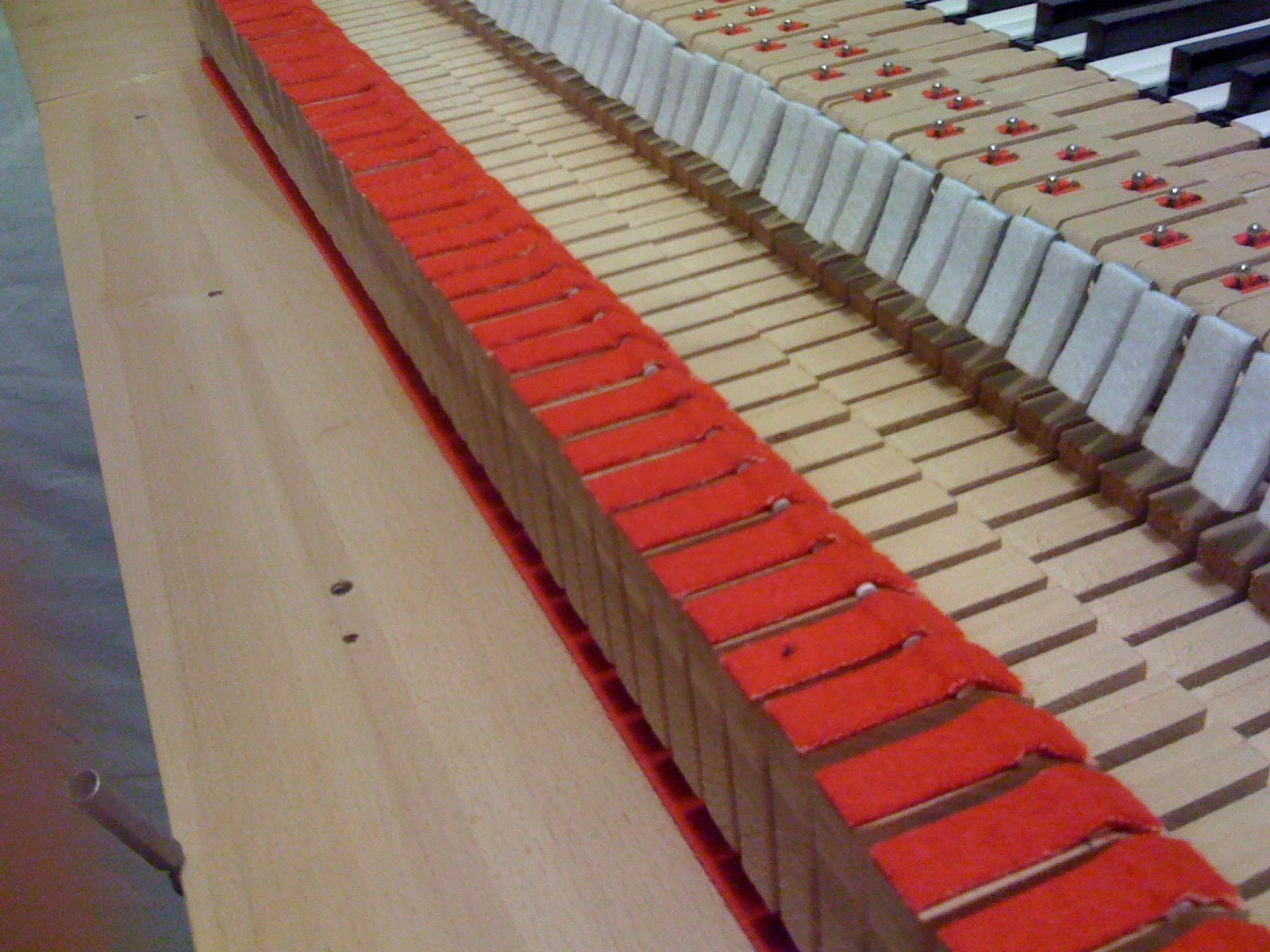
Back Check Mod
The back check mod keeps keys from bouncing back allowing for better
articulation and feel. The instructions from vintage vibe are ok.
However, there are a few extra bits of knowledge I recommend following:
- Drill pilot holes in the keys, I had a few keys split a little bit
around the screw. Even though the video instructions say the pilot
holes aren't needed, do it anyway.
- Sand the back of the hammers where they touch the back checks with
fine grid sand paper. Make em smooth with no burs. This will ensure
the hammers don't drag needlessly on the back checks and slow your
action down.
- Bend the back checks so they sit as high up on the hammer
as possible. Adjust them to avoid the hammer sliding on them to
avoid extra friction. The bottom back check in the pic below is how
I was able to add height.
- Add the back check mod AFTER the Miracle Mod if you are doing
them both. Otherwise, you will need to re-adjust the backchecks again
once the Miracle Mod is installed.
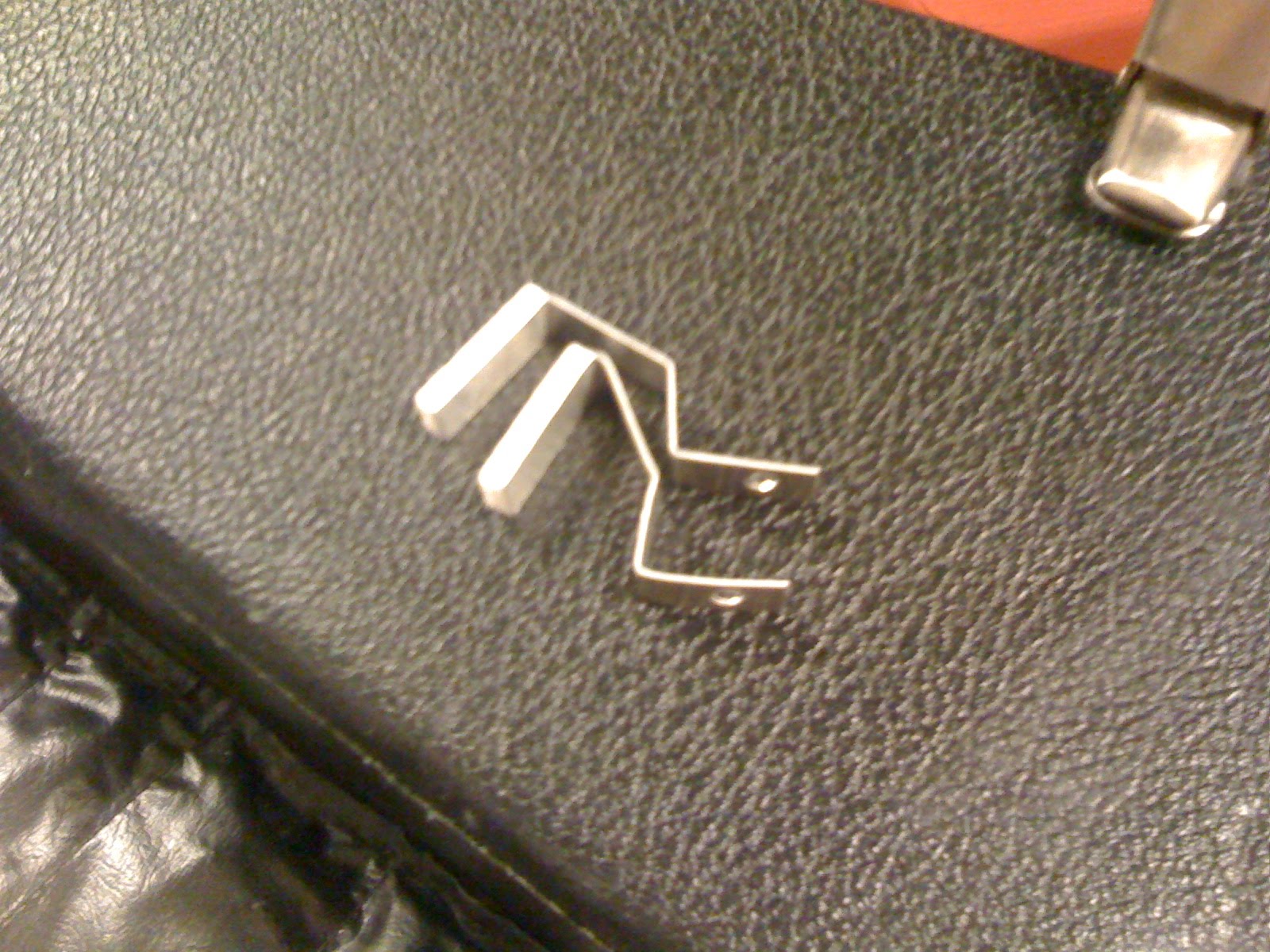
Hammer Tips
Changing out the hammer tips is fairly strait forward and gives a more
consistent and even tone across the keys.
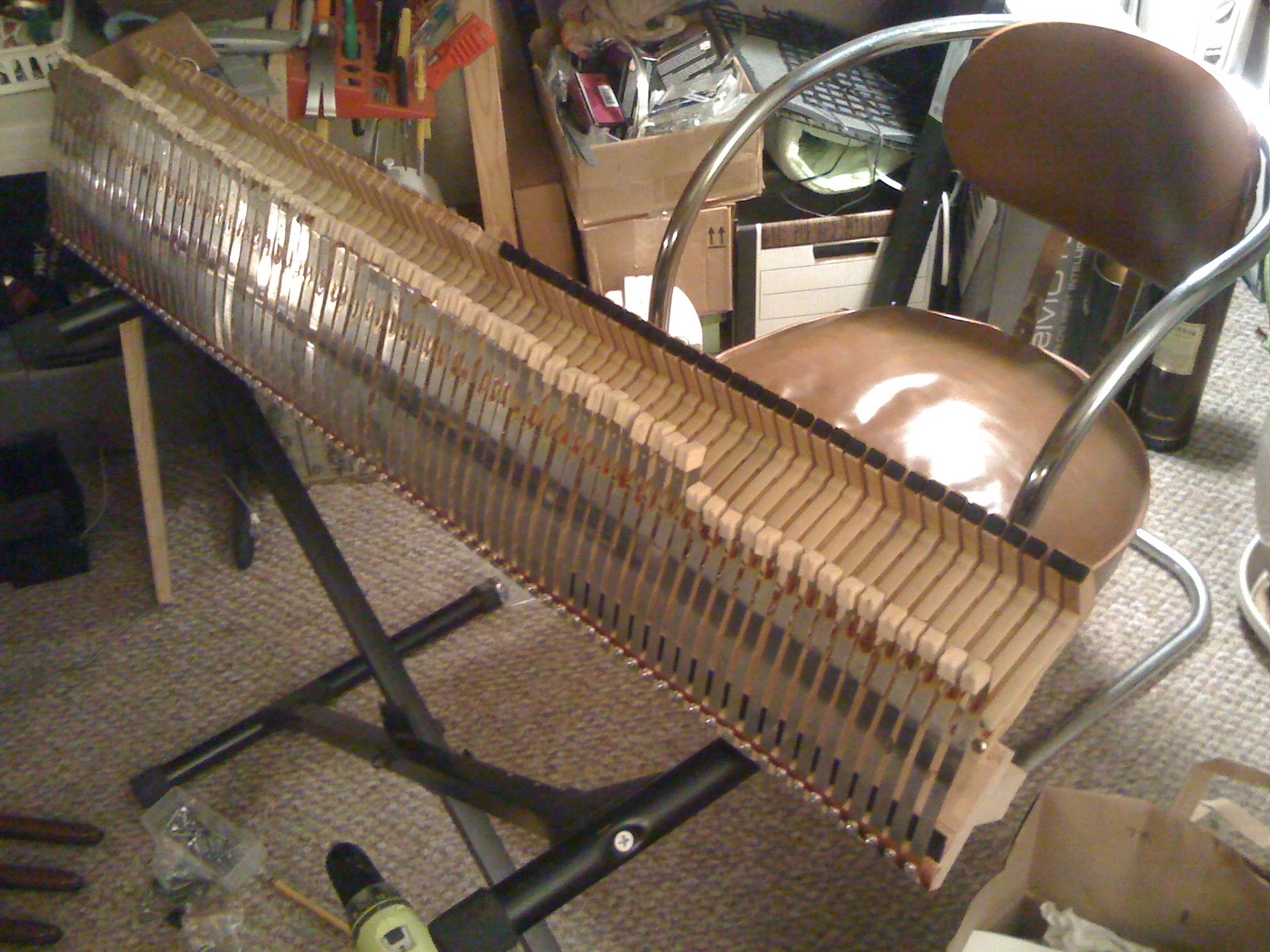
In the Studio
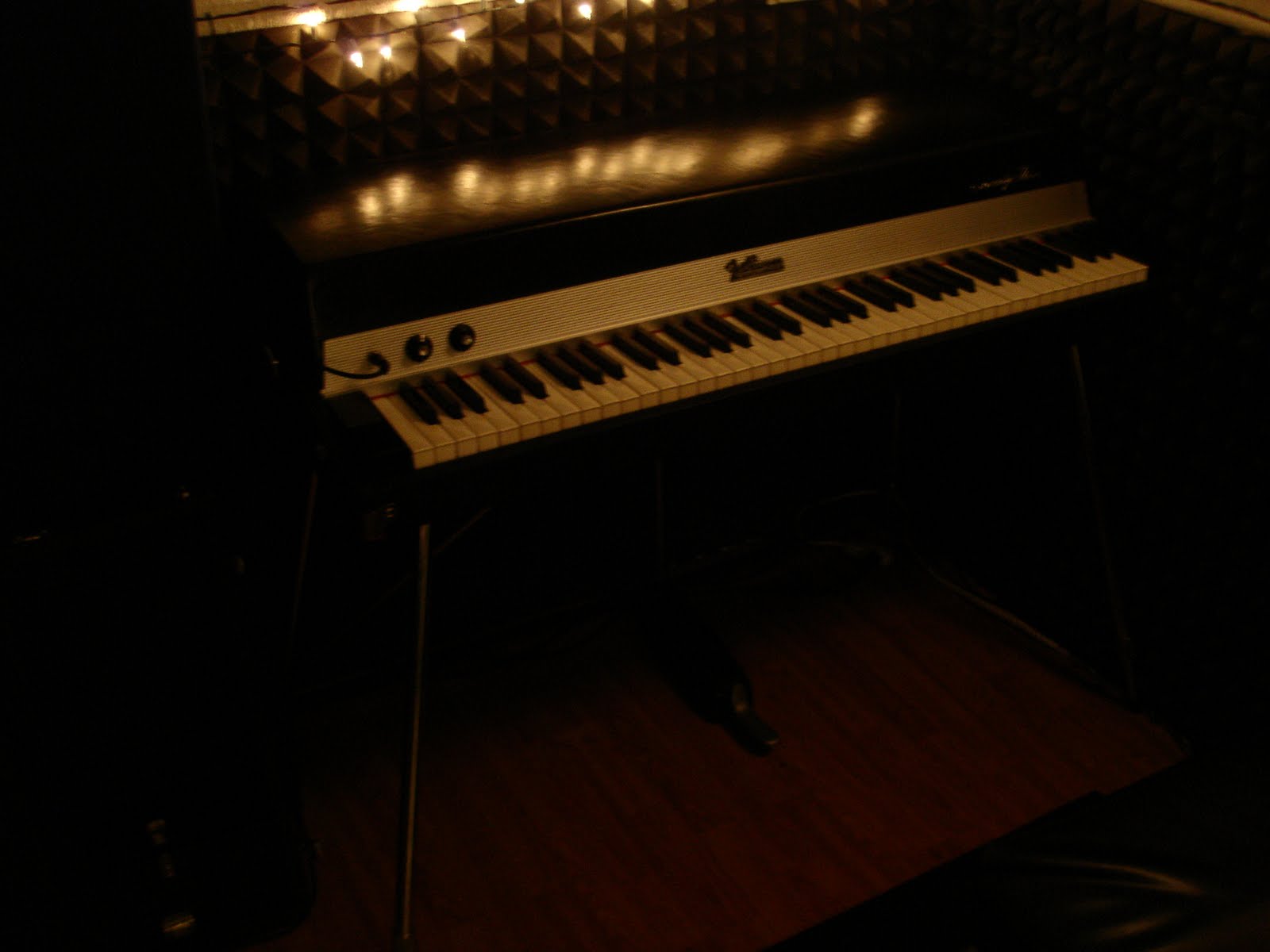
A few months ago I built the bassman version of the Ruby headphone amp
into an Altoids tin (http://www.runoffgroove.com/ruby.html).
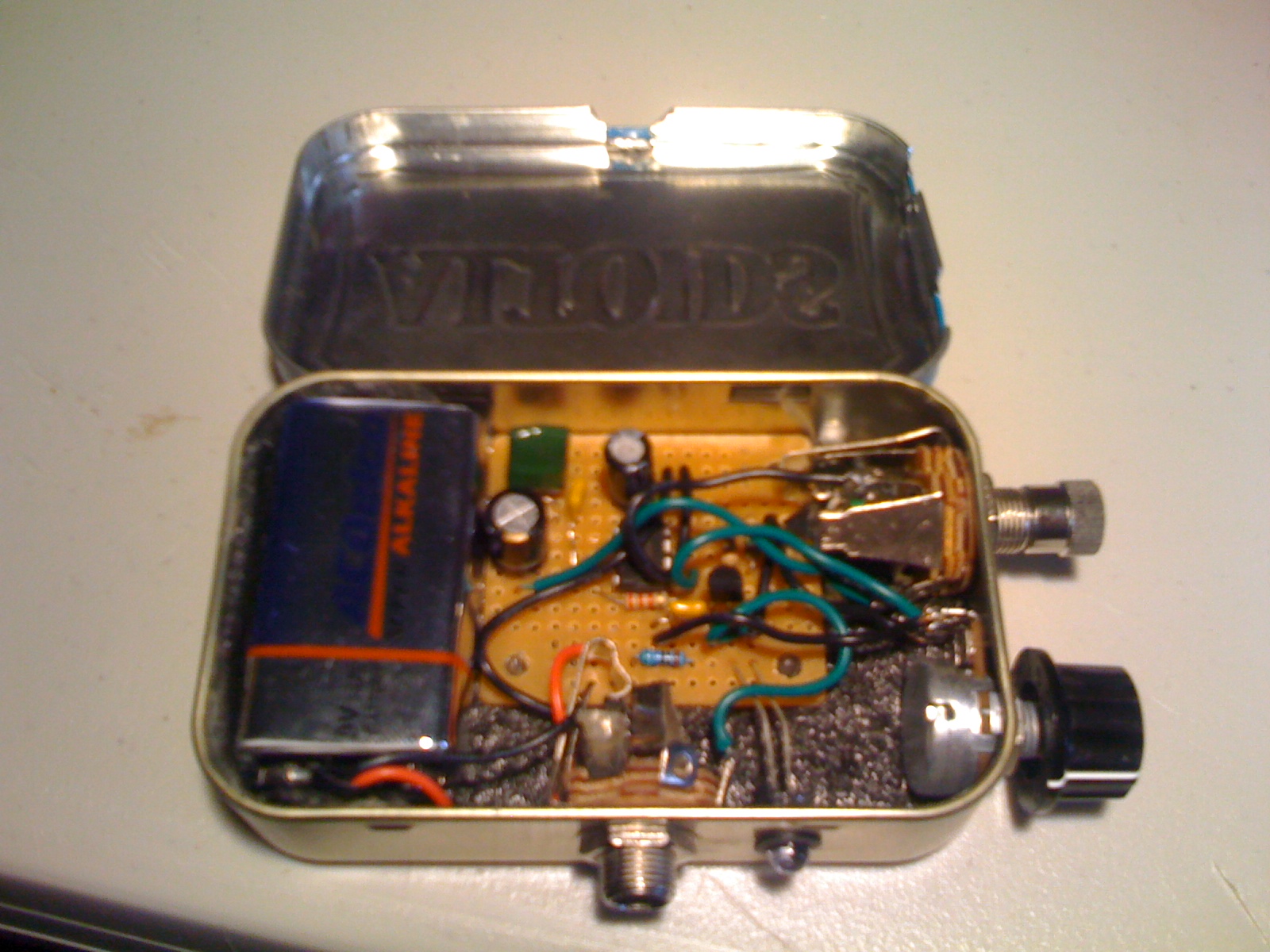
This put me on the constant lookout for project boxes of similar sorts.
The can from the illy espresso I'd been drinking stuck out, and I knew
it was the right thing for the next version which could also house a
small speaker.
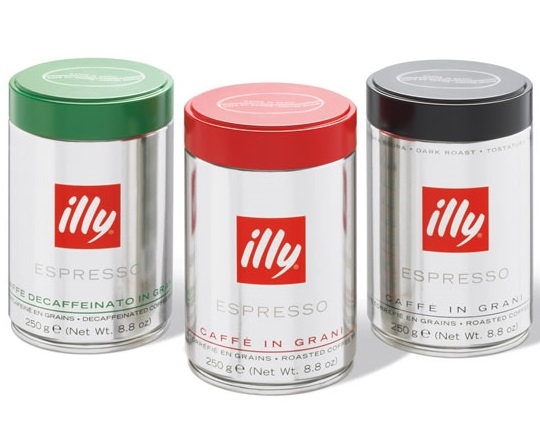
The buildout started with the electronics and I wanted to build the amp on
to a perf board half the size of the one I used for the altoids amp. As
always, soldering all these electronics together can be tedious. The
more planning you do prior to buildout the easier the job is. However,
if you lack experience in a subject matter (in my case electronics) it
takes a certain amount of trial and error to even be able to plan
something.
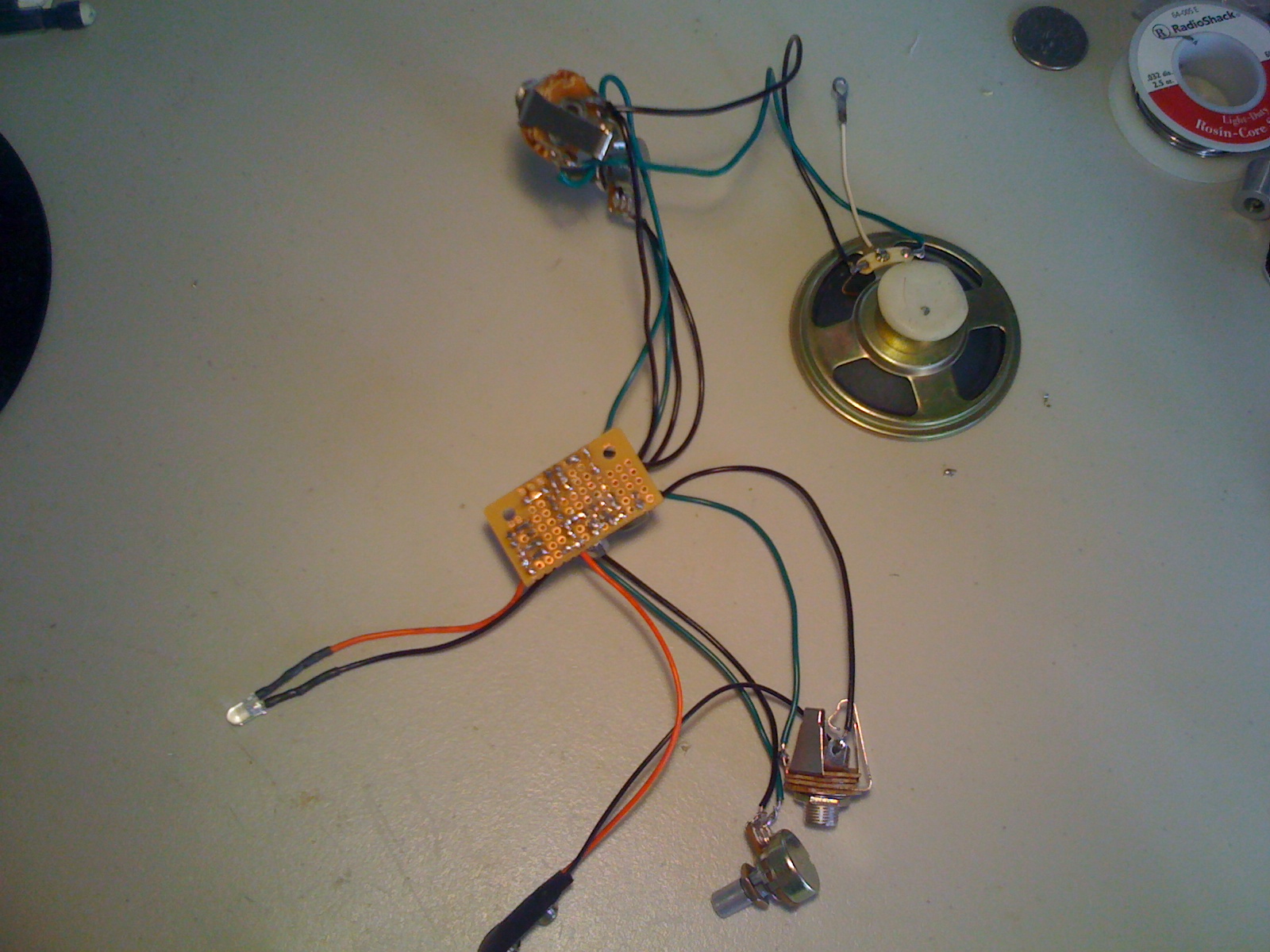
The speaker I bought was about an inch smaller in diameter than the can, so
I needed a large "washer" which could bridge the speaker to the diameter
of the can. I went through a few iterations. Trying to cut a sheet metal
ring resulted in a jaggy nasty thing that cut my fingers up. A CD jewel
case was too brittle and shattered when cut. I finally settled on the
plastic from a DVD case which was soft yet rigid enough for this
purpose.
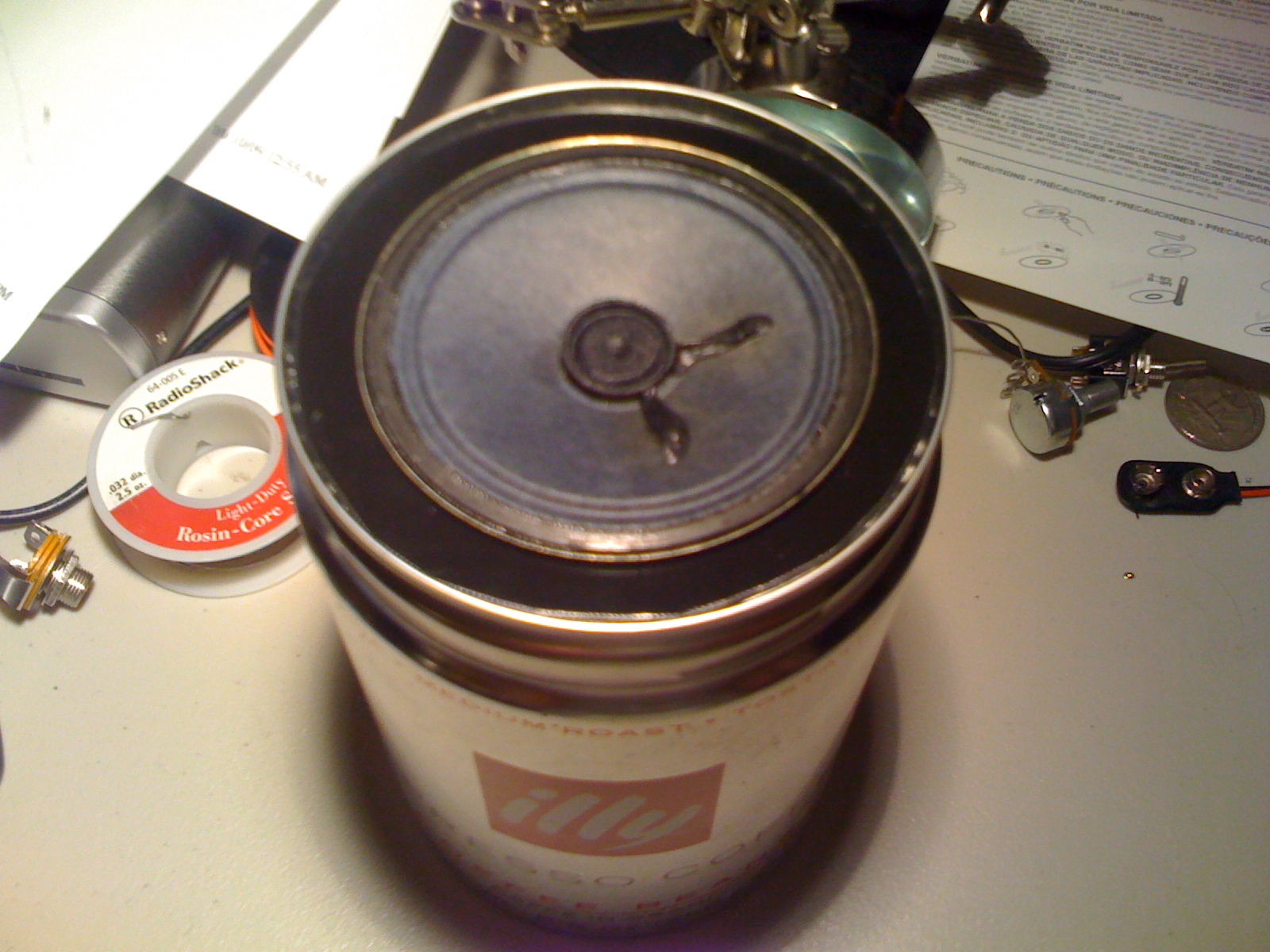
Battery Box
A tricky part of this buildout ended up being the 9volt battery
accessibility.
The bottom is a nice logical spot but how would it be housed and
accessible? I looked online for plastic battery boxes which could
potentially be inserted and slide out for changing the battery. I really
could not find anything that would do what I want or the option was over
priced. I opted to build my own using sheet metal. The design is to
wrap the battery with the metal but have two tabbed edges stick out of
one of the sides that could be screwed into the bottom. I first mocked
up the design with paper and used it as a template for cutting out the
sheet metal. An important part of this was to line the inside with some
left over static foam I had laying around. This kept the battery from
rattling around.
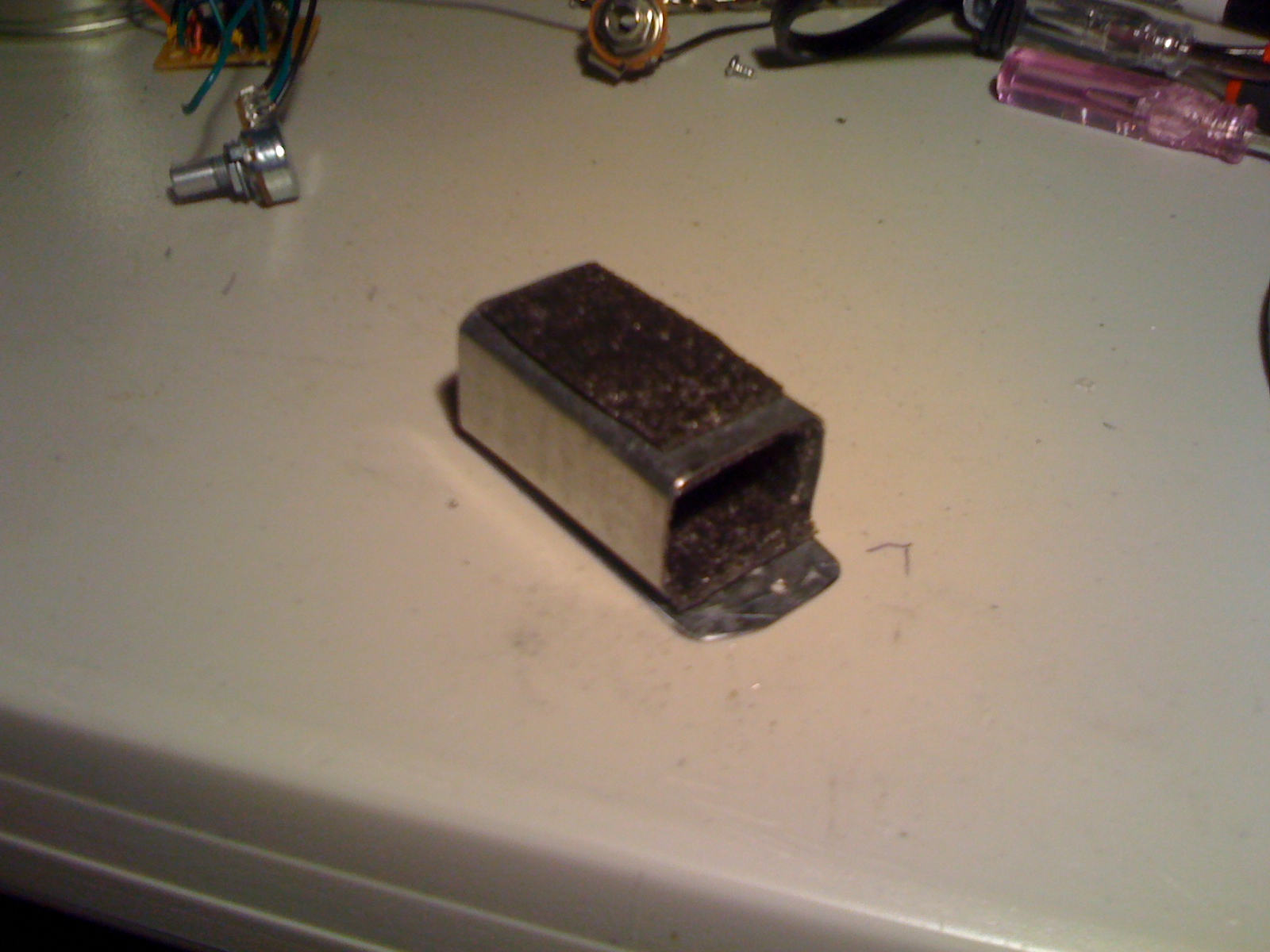
Cutting out the bottom of the can was done by first drilling holes on the
corners and then slicing it up with an exacto knife:
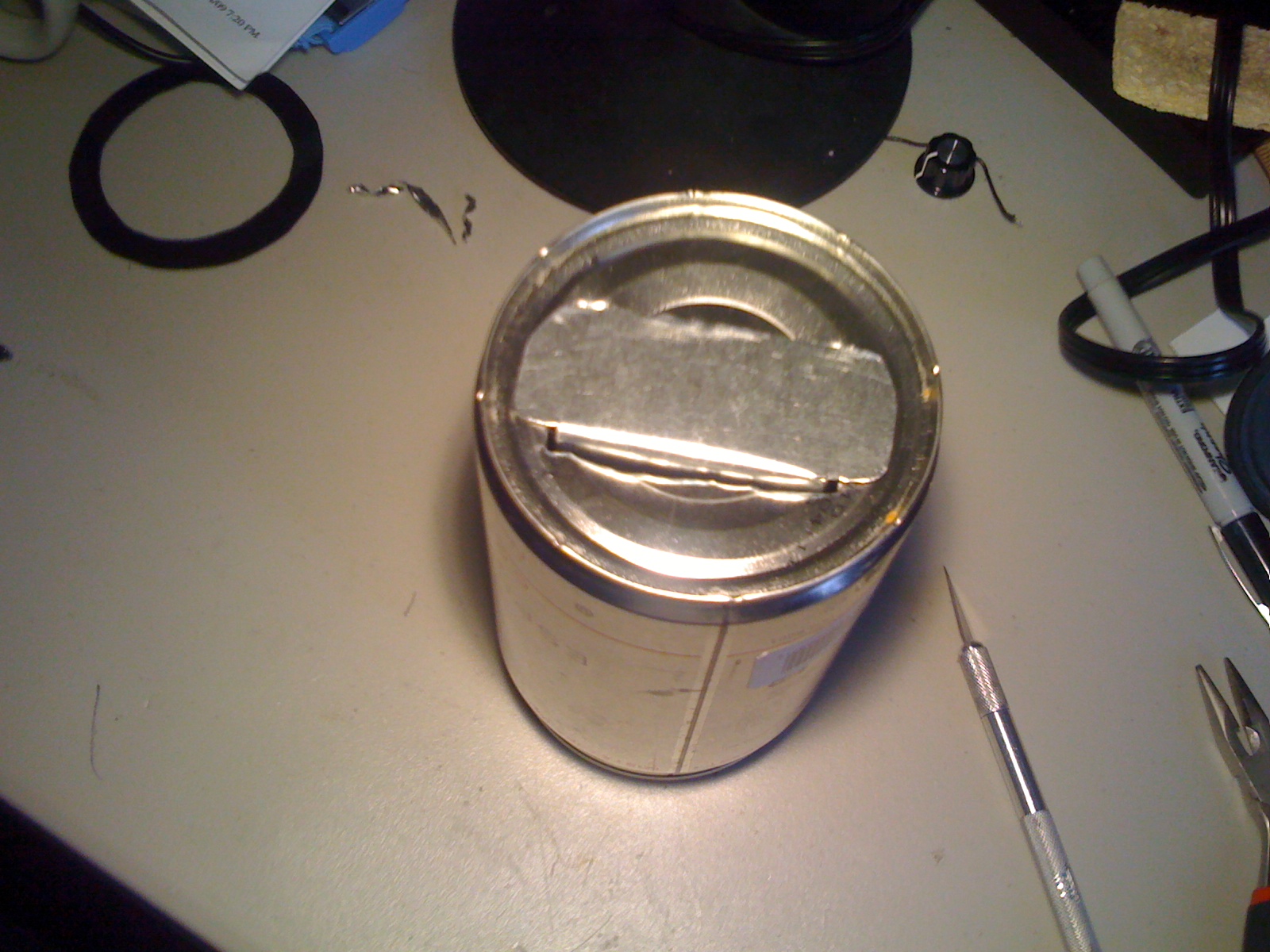
Installing the electronics in the can turned out to be harder than I
thought. Since the knobs and jacks were located at the bottom and my
hand didn't really fit inside the can very well, it was seriously
difficult tightening it all up. I broke wires off the board on more than
one occasion. I decided the top of the battery box was also nice
location of the electronics board since I could pull the board out
fairly easily for potential maintenance.
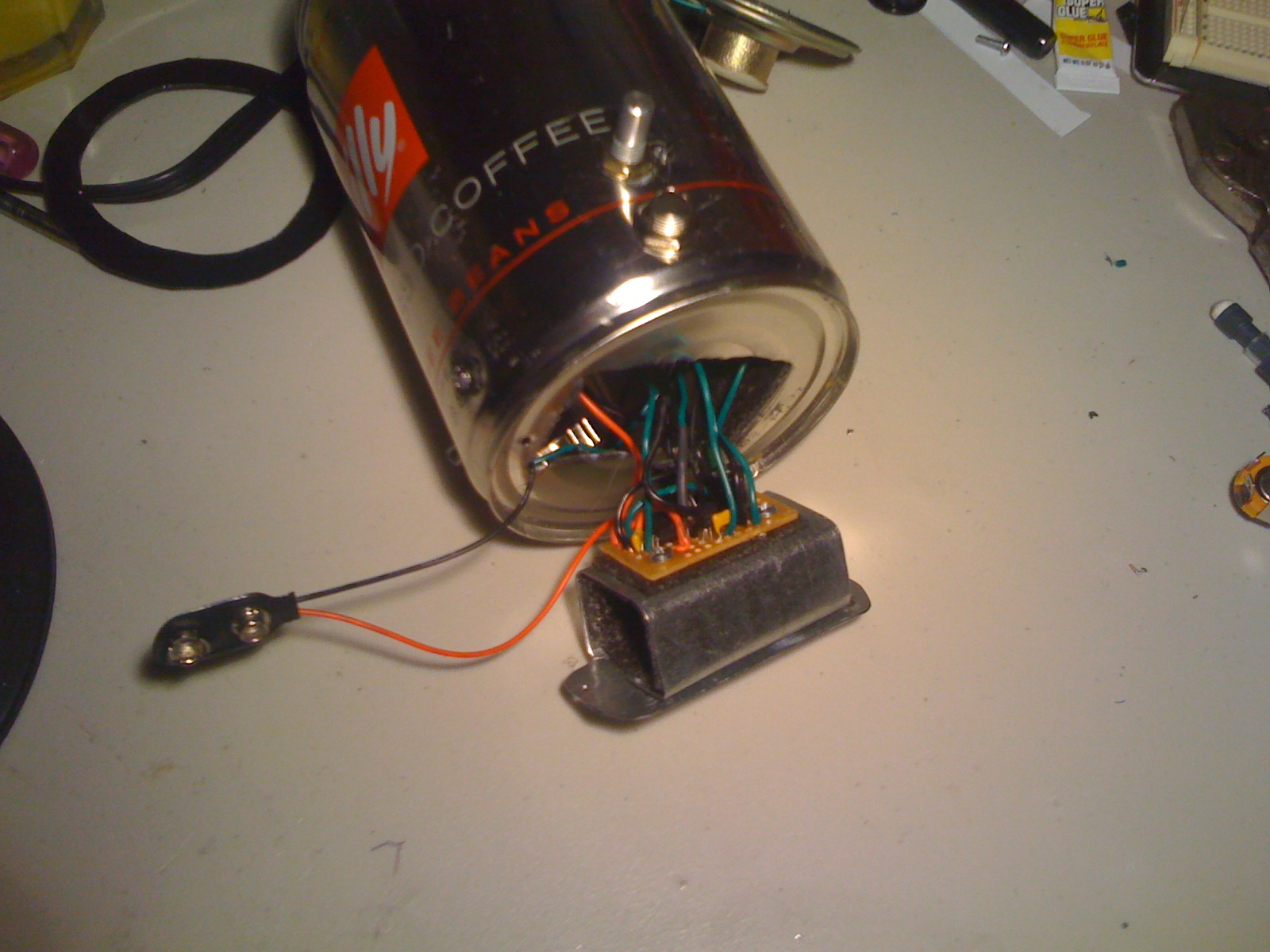
Decals
I wanted to add custom decals that somewhat matched the style of the
existing labels on the can. It took about a week of searching and trial
and error to find the right type of thing to do the job. I ended up
ordering ink jet water slide decals from:
http://www.papilio.com These worked great and
were far better then anything I found at retail stores (office depot and
a handful of hobby/model shops). One thing I did get from a hobby shop
was "microscale liquid decal film". I used this as a clear coat after
printing the labels.
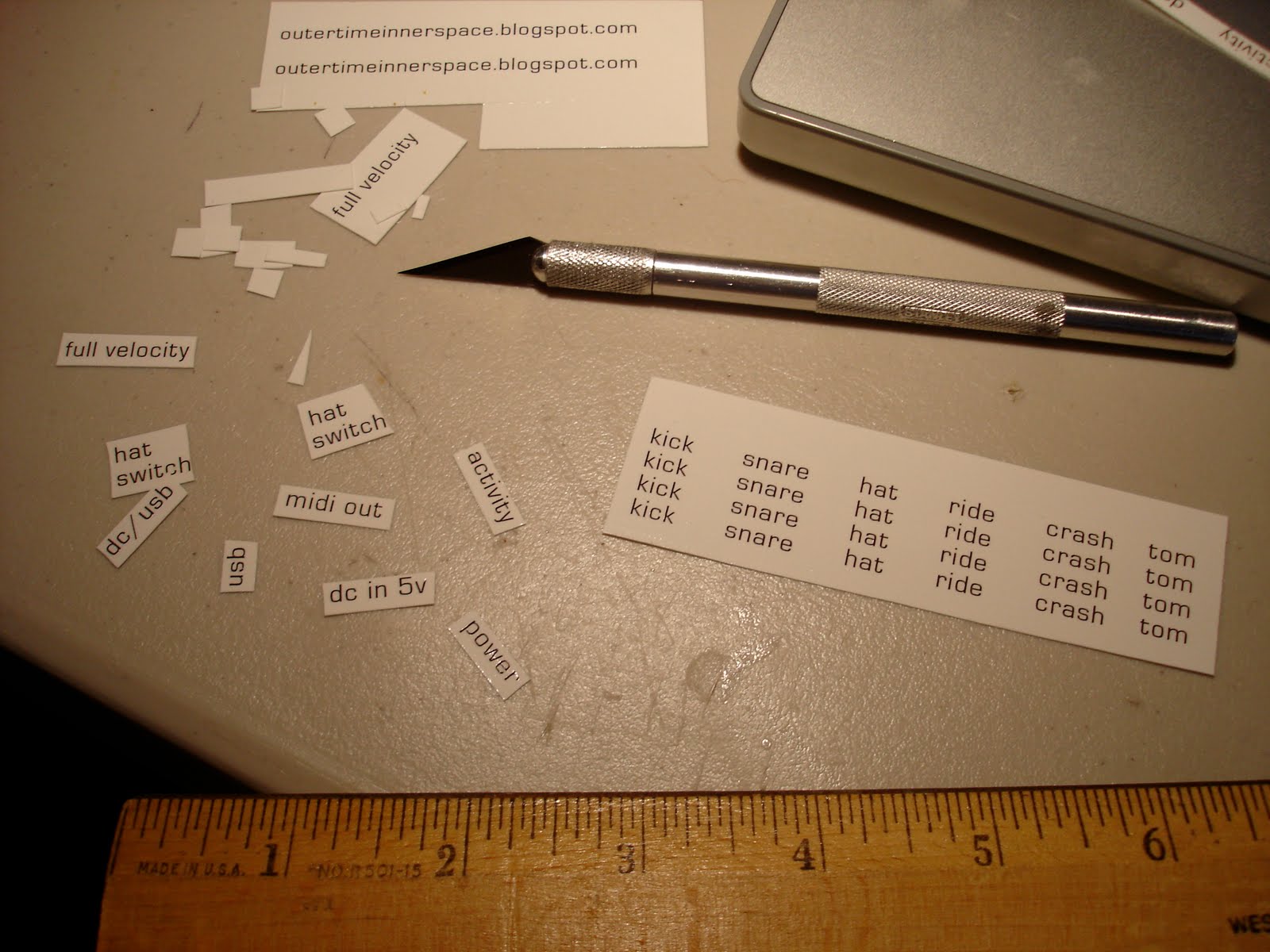
(labels shown are from a different project)
The instructions that come with the paper are
pretty good but here's some extra trial and error I went through.
- Ink only needed to dry for about 15 minutes after printing (these
are small labels)
- Microscale film needed to dry for 15 minutes
- Print extra copies of the label as you can easily screw them up when
sliding onto objects.
- Use a brand new exacto blade to cut out the labels. Otherwise the
edges can stick up a little once the decal is dry.
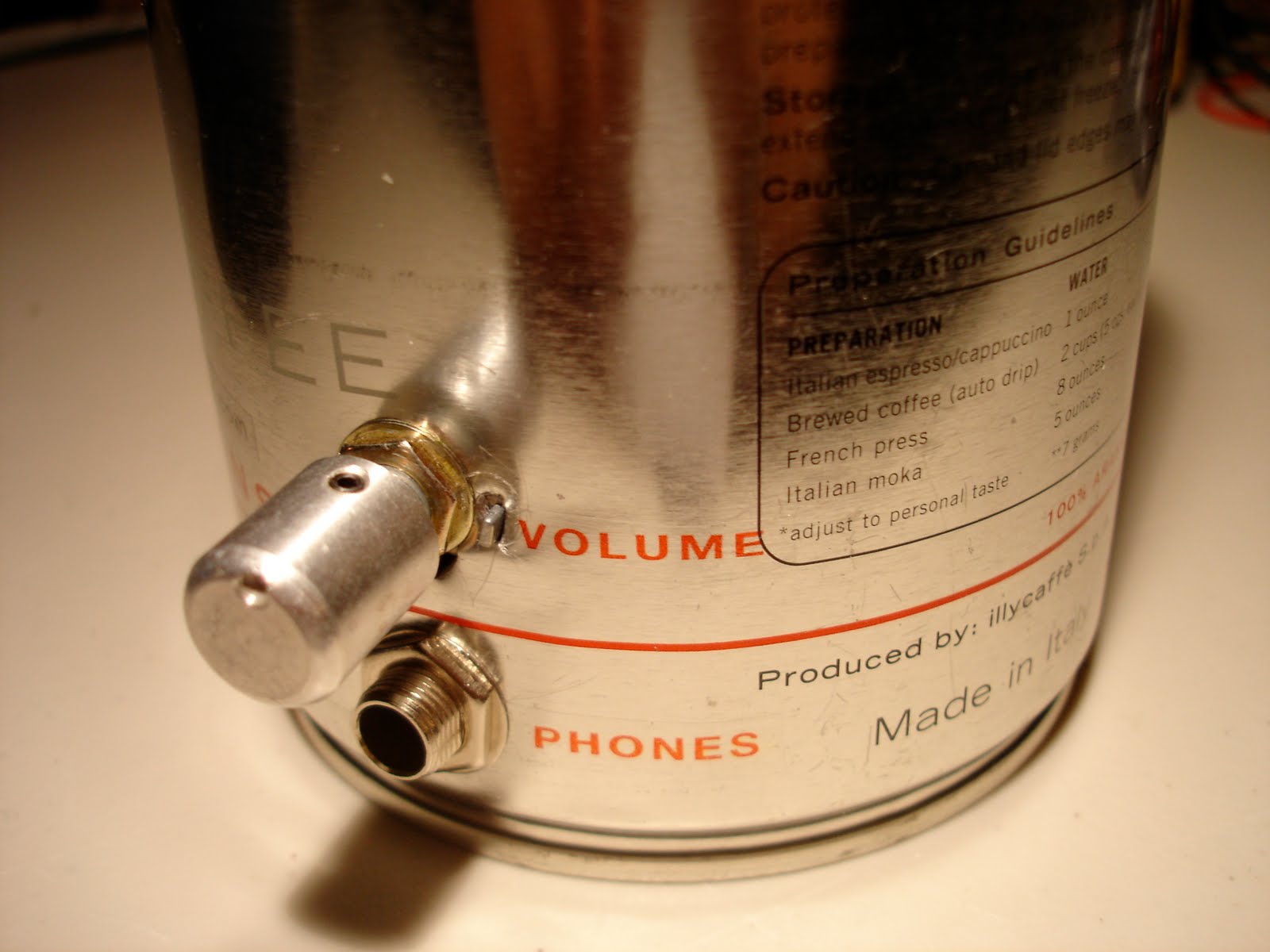
Some of the thoughts I had in regards to usability of the amp:
- No switches. All functions are triggered by plugging cables into the
device. For instance, power turns on when the input cable is in.
Speakers are switched to headphones when headphones are plugged in.
- Keep audio jacks at the the bottom of the can. This would keep the
can from tipping over when a cable is gets pulled on.
- Knobs should be positioned above cables so that the cable does not
get in the way of turning the knob.
- Hide the speaker under the lid.
I also had thought of somehow hiding all the controls under the
lid or on the bottom. But this would have been difficult and I think it
looks cool with the knobs sticking out the sides allowing the original
label to be fully displayed. However, it is a little hard to use this
way because the knobs are hard to turn with one hand (using your right
arm you have to twist your arm to turn the knob on the left side or vice
versa). Having the knobs close together would have been a much better
decision as would allow you to easily tweak combination's of gain and
output volume to get different effects.
Final Product:
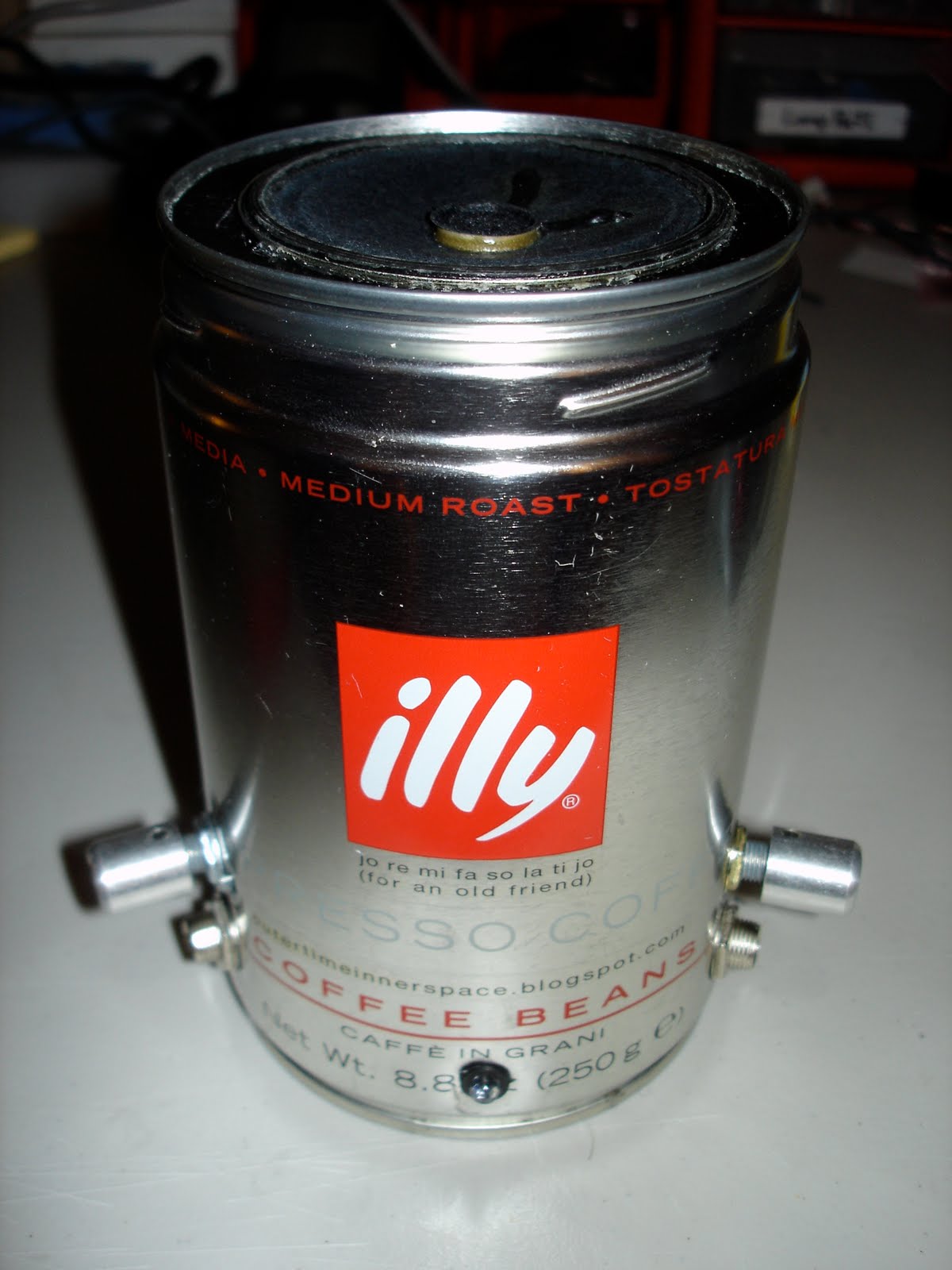